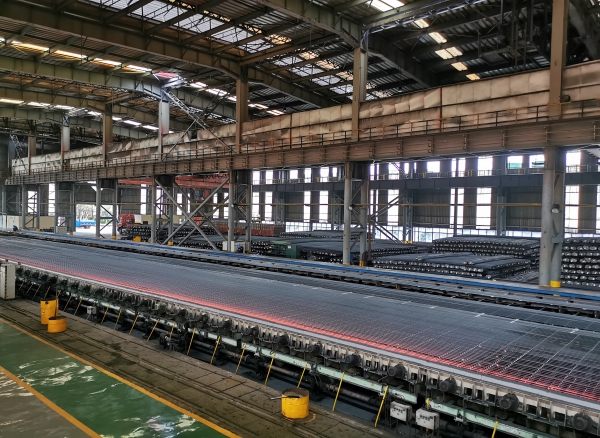
坚持目标导向,制定“硬核”措施。
该单位从精细化管理抓起,不断强化干部作风建设,要求各级管理人员针对重要工作必须做到亲自督办、亲自检查、亲自跟踪、亲自验证,通过夯实责任、量化目标,为实现轧废为零目标奠定坚实管理基础。一方面对标行业先进指标,重新核定各作业区上半年轧废目标,并制定“进军”路线图,通过表单化管理的有效落实,全力突破轧废偏多瓶颈;另一方面,加大操作技能培训频次,强化岗位操作技能,不断提升员工素质素养,与全员签订岗位承诺书,承诺“我的岗位零轧废我的岗位请放心”,通过书面承诺,激发各级人员责任心,从而有效降低轧制废钢率。
坚持问题导向,严格过程管控。
针对前期生产中出现的轧废偏多问题,该单位认真汇总、仔细分析,对每次出现废钢的原因进行追根溯源。从原料接收到钢材出库,该单位对每一道工序都严密监督,切实减少轧制废钢,要求炉号班加强钢坯管理,对保温车转运及辊道输送钢坯加强监测,并及时反馈信息,与炼钢工序沟通协调,避免脱方、裂纹等不合格钢坯入炉;加热炉控制室做好温度调控,把握好出钢节奏,防止粗中轧堆钢;精轧区域做好料型标准控制及轧机装配工作,强化岗位点检巡查,及时发现设备隐患,通过提高设备稳定性,进一步降低各工序轧废。
坚持结果导向,岗位创新促落实。
该单位以“效率、效果、效益”为导向,从过程优化、效率提升等出发,全面开展设备改造、工艺优化等活动,以技术进步促进轧制废钢率降低,先后开展了多项轧制工艺优化提升工作,通过对φ16规格四切分增加多预切,提升生产稳定性;对φ14规格孔型进行优化,解决了尾部堆钢的难题;棒一作业区应用无套轧制,不仅有效减少了活套处废钢,而且可缩短过钢间隙0.5秒;高线作业区实施分钢辊道、大活套程序优化等改造,解决了长期以来靠人工翻钢追尾事故多的瓶颈问题,并分别缩短双线过钢间隙2.6秒。与此同时,该单位还创新研究并应用轧区电流监控报警程序,不仅可及时监控电机异常、连轧关系失衡、断辊等事故,而且可通过电流监控实时判断并第一时间做出调整,为及时处理轧线故障、降低轧制废钢率提供技术保障。
轧废控制是衡量轧制水平的最直接体现,通过一系列措施的有效实施,当前轧废攻关已取得一定成效。后续,该单位将不断向行业标杆看齐,守正出奇、创新赋能,不断降低轧制废钢率,为提升成材率、作业率等技术经济指标提供先决条件,进一步实现高效生产。(赵菲菲)