走进智慧钢城
深冬里的东海岛,寒风凛冽,而宝钢湛江钢铁生产车间内却依然热气腾腾,一炉炉铁水奔腾不息,钢花绚烂地绽放。火红的钢坯在生产线上快速穿过,几十米的高空中,无人化行车也被5G赋予了生命。作为钢铁业高质量发展示范基地,宝钢湛江钢铁肩负起新时代国有企业和钢铁行业的使命担当,以提升企业竞争力,提升“有闲、有钱、有趣”指数,促进员工与企业和谐、幸福发展为目标,推动管理变革与流程再造,夯实简单、高效、低成本、高质量优势,建立钢铁工业互联网平台,赋能高质量发展,努力实现“全产线数字化工厂”、劳动效率全面提升,打造智慧钢厂新标杆。
近年来,宝钢湛江钢铁在智慧制造上收获了一份靓丽而又来之不易的成绩单:.截止2021年厂区总共投运超150台套工业机器人,打造了行业首创水系统集中管控平台、投运全球首台3600吨/小时智能化连续式卸船机、全球首套智慧铁水运输系统上线......“1550冷轧智能车间”获得2018年广东省“智能制造试点示范”称号,钢制品智慧物流入选工信部防疫抗疫复工复产解决方案。在推进“5G+智慧钢厂”项目建设中,宝钢湛江钢铁摘得广东省首批“5G+工业互联网应用示范园区”牌匾,荣获第四届“绽放杯”5G应用征集大赛标杆赛金奖。这些闪烁的“智慧之光”,在湛钢的“ONE MILL”智慧制造畅想中,已经成为一个个跃动的音符。
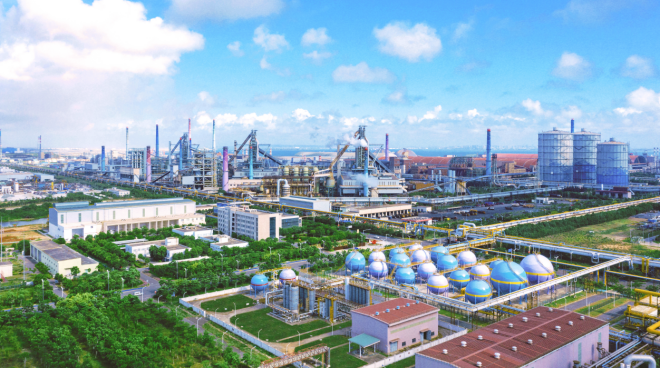
湛江钢铁厂区大景
以数据为中心,创新整体架构
智慧制造,是将新一代信息技术与工业制造相结合,带动生产、管理、服务的进一步自动化、数字化和智能化。近年来,宝钢湛江钢铁以中国宝武智慧制造建设为契机,逐步明确了智慧制造工作思路:坚持价值为本、成熟优先、实用优先、急用优先原则,以提升管理效率、劳动效率、资源配置效率等为准绳,培育了一批具有可复制、可推广的数字化转型技术、管理模式和流程制度。制定了以“四个一律”为目标的智慧制造实施路径,即现场操控室一律集中、操作岗位一律采用机器人、运维监测一律远程、服务环节一律上线。
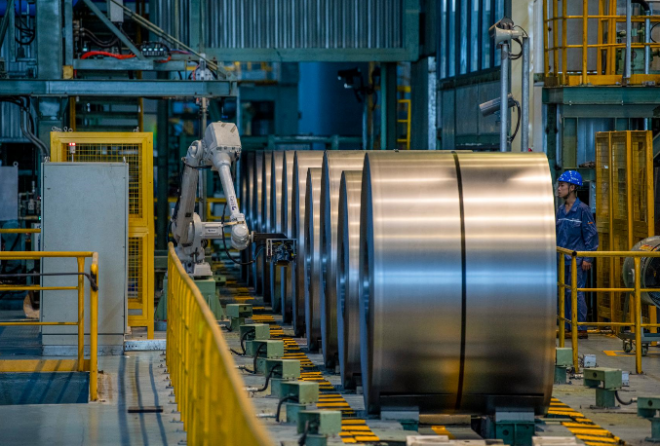
图为工业机器人
“四个一律”既涉及现场装备和集控,也涉及钢铁生态圈的协同和服务。结合生产制造基地实际,宝钢湛江钢铁通过顶层设计划分智慧物流、智慧质量、智慧设备、智慧能环、智慧安保五大平台建设,以组织变革、流程变革、决策变革为抓手,打造全产线数字化工厂。
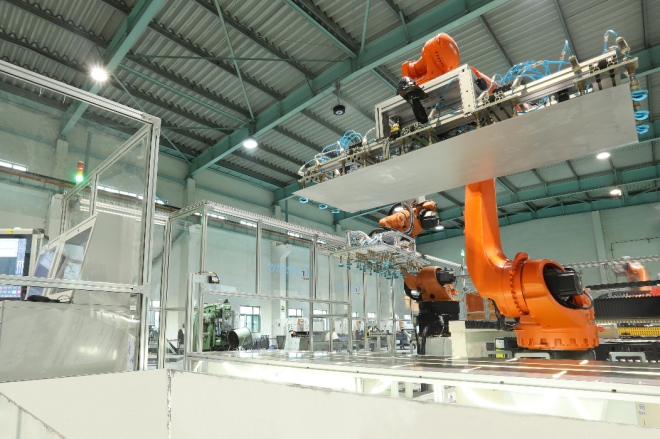
图为工业机器人
以现场为重心,实现创新突破
“智慧制造,要消灭的是什么?正是那些‘3D’岗位(危险性高、劳动环境差、简单重复劳动的岗位)。智慧制造要创造的是什么?是高端的、创造性的岗位。”宝钢湛江钢铁近年来坚持理念创新、技术创新、模式创新,以追求极致效率探索和打造了一批示范项目,让职工在工作岗位上拥有更多幸福感、更多创造力。
坚持理念创新就是要打破传统思维,真正实现现场高效化,湛江钢铁打造全球首个智慧铁水运输系统就是典型案例。该项目由湛江钢铁与中冶赛迪共同研发,将运输与生产紧密结合,形成铁水运输智能化调度,能够实现机车运输全天候环境感知、障碍物精准识别、自动摘挂钩等,AI决策大脑能自动“机车匹配路径最短、任务下发时机最优、路径选择效率最佳”,让TPC效率稳定4.3以上,进一步解放劳动生产力,成为无人驾驶技术在钢铁工业场景的一项突破性实践。
坚持技术创新。按照新发展理念,利用数字孪生与人工智能的核心技术,实施焦炉机车无人化系统的改造,实现了焦炉四大车上升管系统、清门清框、浇浆等自动化操作,达到无人化与操作室远程应急指挥。湛江钢铁建设了无人化智慧化料场,现场25台堆取料机、卸料小车和刮板机全部实现了自动运行,劳动效率、运行效率大幅度提升。湛江钢铁还打造了宝钢股份首基于大数据中心的智慧质量系统,实现从用户需求识别到用户使用,从定性向定量,从事后向预防转变。系统上线后同品种结构质量较大提升,累计产生效益每年超千万元。

无人化鱼雷罐车
坚持模式创新。以业务界面整合、提高劳动效率、降低制造成本为目标,通过智慧集控实现“居一隅而控全局”。湛江钢铁打造了行业首创的水系统集中管控平台,通过技术使操作室“十五合一”,实现全厂“水量平衡一张表、生产管控一幅图”,劳动效率提升50%以上,吨钢耗水成为行内最低。湛江钢铁还积极开发热轧“1+N”智能轧制技术,当前全自动化轧钢模型达到97%以上,基本实现“零干预”生产。同时以智慧制造手段赋能打通两条热轧产线的前后库区、操作室一律集中,培育员工专业互通、技能互通,构建两条热轧产线一体化生产新模式,为湛江钢铁劳动效率引领世界一流奠定坚实基础。
以5G为动能,打造行业标杆
随着5G迈向商业、工业应用,万物互联正在从愿景变为现实,敏锐的湛钢人捕捉先机、顺势而为,积极探索“5G+智慧钢厂”建设新模式,助力钢铁业高质量发展。湛江钢铁利用5G大带宽、低时延、确定性网络性能,在全厂安装370余套5G+工业高清摄像头,赋能企业一、二级高危检修项目、施工现场安全行为观察、边检防疫监控、超低排放环境监控等应用,“足不出户”就能全天候、全方位实施监控。安全升级后,员工现场安全巡检时间可节约15小时/天,及时发现查违纠违456次。
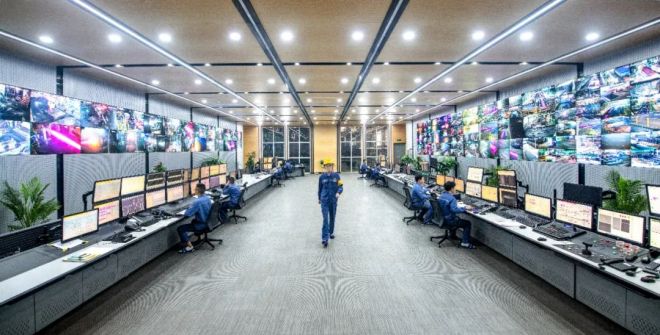
连铸集控中心
湛江钢铁组建了智慧设备团队,通过对全厂原离散化数据信号进行采集、基于预知维修的设备维修工程师体系进行挖掘分析,实现生产要素和设备状态的全生命周期管理,用数字化驱动全厂物质流、能量流和信息流,打造5G+设备在线监测平台,实现了全厂近10万个设备点位数据在线运维,设备点检劳动效率大幅度提升,确保设备运行的安全、稳定、高效。
打造行业内首条5G信号控制生产的热处理线。湛江钢铁先行先试,在无任何相关案例的参考下,与广东联通、中兴通讯高效协同,攻克了21个自动化系统间5种通讯协议转换,打通了10余个网络节点,最终将时延控制在50ms以内,实现了有线和无线的全面融合,生产作业效率翻一番,成为行内5G生产控制示范应用。
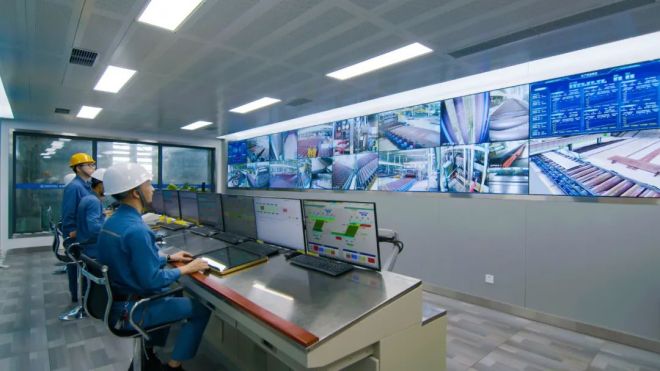
厚板厂5G热处理线操作室
当前,湛江钢铁已验证了35个5G+应用场景,其中26个应用已正式上线,基本覆盖了工信部发布的20个“5G+工业互联网”典型应用场景中的12个,包括远程设备操控、设备故障诊断、器视觉质检、无人智能巡检等。未来,我们还将在厂区智能理货、生产单元模拟、精准动态作业、工艺合规校验、生产过程溯源等领域深入研究,并对已涉入的领域进行应用拓展,利用5G技术打造成钢铁行业新标杆。
接续奋斗,未来可期。湛江钢铁将把智慧制造和员工对美好生活的向往结合起来,不忘初心、肩负使命,推进数智化钢铁事业奋勇向前,使湛江钢铁成为数字化科技型企业引领者示范者,最终打造成为世界最高效率的绿色碳钢制造基地,为中国宝武成为世界一流伟大企业贡献力量。
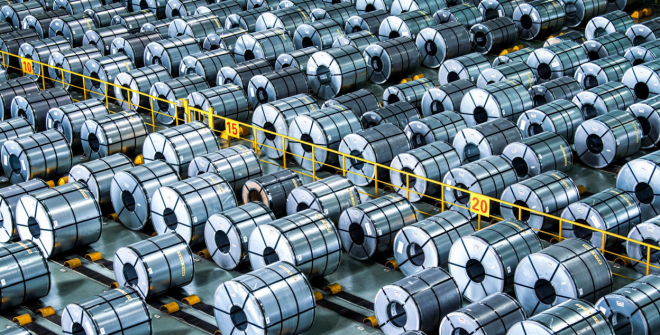