为了探寻微晶石墨替代鳞片石墨在含碳耐火材料中应用的可行性,以烧结板状刚玉、鳞片石墨、微晶石墨、Si 粉、SiO2粉和α-Al2O3粉为原料,以热固性酚醛树脂为结合剂混合均匀后,在150 MPa 压力下压制成25mm×25 mm×140mm 的长条试样,经220℃保温24 h 后制备不烧Al2O3-C 试样。研究了微晶石墨加入质量分数分别为0、2%、4% 和6% 对不烧Al2O3-C 耐火材料性能的影响。结果表明: 随着微晶石墨加入量的增加,试样的体积密度略有升高,常温抗折强度和耐压强度稍有提高,高温抗折强度有所增加,抗热震性稍有提高,抗渣侵蚀性有所下降。
石墨材料的制备也是矿物和材料领域的研究热点之一,其原料包括无烟煤、石油焦和微晶石墨等。其中,微晶石墨是一种具有潜在用途的资源。虽然微晶石墨晶粒尺寸小,有晶格缺陷,抗氧化性能弱于鳞片石墨,但在各向同性、反应活性和某些力学性能等方面优于鳞片石墨。因此,微晶石墨的开发与利用成为近年来本领域的研究热点。
由于连铸技术的广泛应用,使得钢水温度提高,钢水停留时间延长以及钢水搅拌激烈,这些都要求耐火材料具有较高的高温强度以及良好的抗热震性、抗钢水冲刷和抗侵蚀等性能。为满足连铸工业的技术要求,从20 世纪70 年代开始,人们将石墨等碳材料引入到耐火材料中,形成氧化物-碳复合材料。最为常见的就是铝碳耐火材料,被广泛应用于连铸和滑板用耐火材料。后来,为了提高铝碳耐火材料的性能并延长其使用寿命,人们在碳源、添加剂、碳纤维等对含碳耐火材料性能的影响方面做了很多研究。
传统含碳耐火材料中的石墨基本都采用鳞片石墨。随着优质鳞片石墨的日渐匮乏,探寻微晶石墨在含碳材料中应用的可能性也就显得日趋重要。这不仅可以拓宽微晶石墨的应用领域,获得较好的经济效益,而且还可以保护鳞片石墨的开采。在本工作中,尝试在铝碳材料中引入微晶石墨,研究了微晶石墨替代鳞片石墨后对材料性能的影响。
试验
原料:
试验所用主要原料:板状刚玉( 3 ~ 1、1 ~ 0.5、0.5 ~ 0.088、≤0.088 mm) ,Si 粉( ≤0.088 mm) ,鳞片石墨( ≤0.154 mm) ,郴州微晶石墨( ≤0.154 mm) ,α-Al2O3粉( ≤0.088 mm) ,SiO2粉( ≤0.088 mm) 。原料化学组成见表1,两种石墨的化学组成见表2。
鳞片石墨呈片状,晶体表面光滑,晶粒尺寸约50μm; 而微晶石墨呈粒状,它的颗粒由许多随机取向的微小晶体聚集而成,晶粒尺寸小,约227nm,晶粒表面粗糙,晶粒缺陷大。因此,推测微晶石墨的反应活性比鳞片石墨的高,各向同性比鳞片石墨的好,用在含碳耐火材料中能改善耐火材料的某些性能。
制样及性能测试
按照表3 配料。将配好的物料以热固性酚醛树脂为结合剂,用爱立许搅拌机混6min,然后将混均匀的原料在液压机上以150 MPa 的压力成型为25 mm × 25 mm × 140 mm 的长条状试样,于220 ℃固化24 h 后备用。
按照GB /T 2997—2000 检测试样的体积密度和显气孔率; 按照GB /T 3001—2007 对试样进行常温抗折强度测试; 按照GB /T 5072—2008 对试样进行常温耐压强度检测;按照GB /T 3002—2004 检测试样的高温抗折强度(1400 ℃埋碳保温0.5 h) ; 在1100 ℃( 空气气氛) 下利用水淬冷法测试试样经3 次热震后的残余抗折强度,以强度保持率表征抗热震性; 采用动态感应炉法来评测试样的抗渣性: 将在220 ℃固化24 h 后的长条状试样固定在模具里,然后向模具里倒入刚玉- 尖晶石浇注料,经振动成型为一个圆柱形坩埚,这样,长条试样就固定在坩埚壁上,其截面图如图1所示,然后装入感应熔炼炉。将6 kg 普通钢放入坩埚中并加热至钢完全熔化,加入200 g 左右的钢包渣( 化学组成如表4 所示) ,待钢块与熔渣完全熔融,于1600 ℃保温30 min 停炉冷却至室温,之后用扫描电镜观察侵蚀后试样的显微结构,并结合EDS 对侵蚀后试样的微区经行分析,用Image-Pro Plus 6.0 统计渗透层中渣区域百分比,用Factsage 软件分析侵蚀后试样渗透层中渣的黏度。
结果与讨论
常温物理性能:
从图3 可以看出,当试样不加微晶石墨时,试样的显气孔率为21%,体积密度为2.71g·cm - 3;随着微晶石墨加入量的增加,试样的显气孔率稍有下降,体积密度略有提高。当试样中的微晶石墨加入量为6%(w) 时,试样的显气孔率为18.7%,体积密度为2.85 g·cm -3。当不加微晶石墨时,试样的抗折强度为2 MPa,耐压强度为14 MPa,随着微晶石墨加入量的增加,试样的抗折强度和耐压强度有所提高,当微晶石墨加入量为6%( w) 时,试样的抗折强度为4 MPa,耐压强度为33MPa。这是因为微晶石墨的晶粒尺寸小,晶粒表面粗糙,在成型时能更好地填充在试样骨料之间的空隙中且不易滑动。
高温性能:
高温抗折强度:在1400℃埋碳保温0.5h条件下, 随着微晶石墨加入量的增加,试样的高温抗折强度呈上升趋势。当试样不加微晶石墨时,试样的高温抗折强度为5 MPa,当试样中的微晶石墨加入量为6%(w) 时,试样的高温抗折强度为7 MPa。这得益于一方面微晶石墨呈粒状,表面粗糙,成型后微晶石墨能更好地填充在试样的空隙中且不易滑动;另一方面,可能是微晶石墨的晶粒小,晶粒缺陷多,表现出较大的活性,在高温下更容易与试样中的Si 反应形成SiC,从而提高试样的高温力学性能。
抗热震性:1100℃水冷3次热震后的条件下,随着微晶石墨加入量的增加,试样的强度保持率呈上升趋势,材料的抗热震性有所提高。当试样中的微晶石墨加入量为0 时,试样的残余抗折强度为0.4 MPa,强度保持率为20%; 当试样中的微晶石墨加入量为6%( w) 时,试样的残余抗折强度为1.4 MPa,强度保持率为35%。这是因为鳞片石墨易发生择优取向,使得材料平行于成型压力方向和垂直于成型压力方向的热膨胀系数、热导率等产生显著差异,从而表现出各向异性,而微晶石墨颗粒是由许多随机取向的微小晶体聚集而成,表现出各向同性,当试样中引入微晶石墨后,鳞片石墨的这种择优取向得到明显改善,从而提高了材料的抗热震性。
抗渣性:试样A3的侵蚀缺口较大。经测量、计算得出: 试样A0 的侵蚀指数为9.51%,渗透指数为7.39%;试样A3 的侵蚀指数为14.69%,渗透指数为10.82%。说明试样A3的抗渣性较差。
试样A0 和试样A3 经1600 ℃试样A0 基质中渣的面域百分比约为6.8%,试样A3 基质中渣的面域百分比约为8.2%。根据表5 各点EDS 分析结果,用Factsage 软件算得试样A0 基质中渣的平均黏度为0.66 Pa·s,试样A3 基质中渣的平均黏度为0.54 Pa·s。这是因为在侵蚀试验过程中,随着温度升高,试样中C 会被氧化形成微孔,而微晶石墨的抗氧化性比鳞片石墨差,使得试样A3中形成的微孔要比试样A0的多,导致试样A3 的结构较为疏松,加速了渣向试样A3 中的侵蚀,使得更多的渣渗透到试样内部。另外,微晶石墨中杂质含量较多,高温下这些杂质会与试样反应,使试样侵蚀程度加深。
结论
微晶石墨晶粒尺寸小,晶粒表面粗糙,易成型,随着微晶石墨含量的增加,试样的体积密度和常温强度有所提高。
微晶石墨晶粒小,晶体缺陷多,表现出较大的活性,高温下易与Si 反应生成SiC,提高了试样的高温抗折强度。
微晶石墨的各向同性比鳞片石墨好,微晶石墨的加入提高了试样的抗热震性。
相比鳞片石墨,微晶石墨抗氧化性差且杂质含量较多,微晶石墨的加入降低了试样的抗渣性。
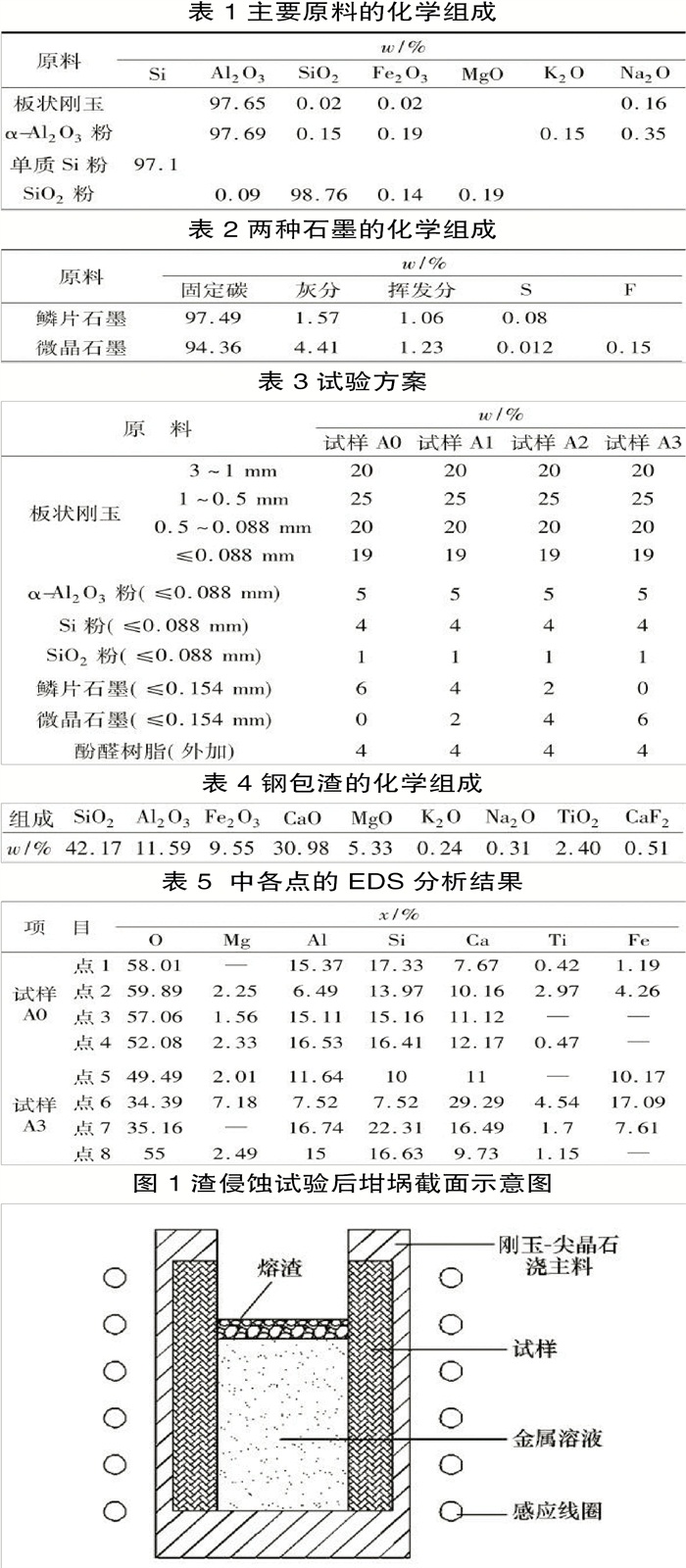