中国冶金报 中国钢铁新闻网
李超群 报道
甘泉 摄影
走进智慧钢城
随着“数字化、网络化、智能化”工业系统意识在全世界范围得到认可,近年来,重庆钢铁聚焦极致效率、节能减碳,加大智慧制造投入,呈现出了蓬勃发展的新局面。
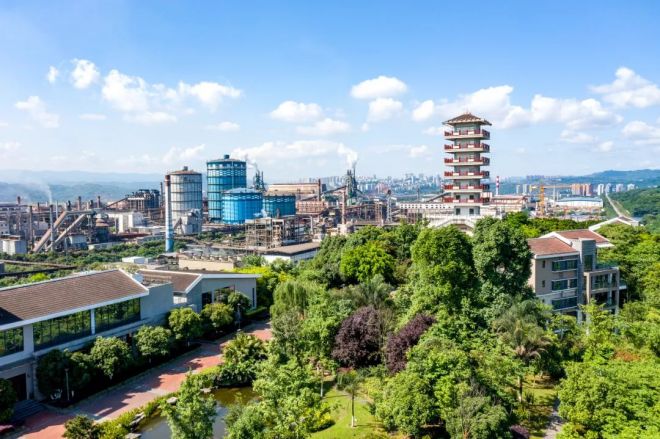
跑出 “智慧加速度”
早在2019年,重庆钢铁就制定了智慧制造规划方案, 2020年7月,重庆钢铁对接中国宝武“宝武工业互联网生态平台”的需求,开启了新一轮的智慧制造“3+2”五年行动方案编制,围绕“打造超千万吨高质量绿色智造钢铁企业”的战略目标,全面推进重点项目建设。
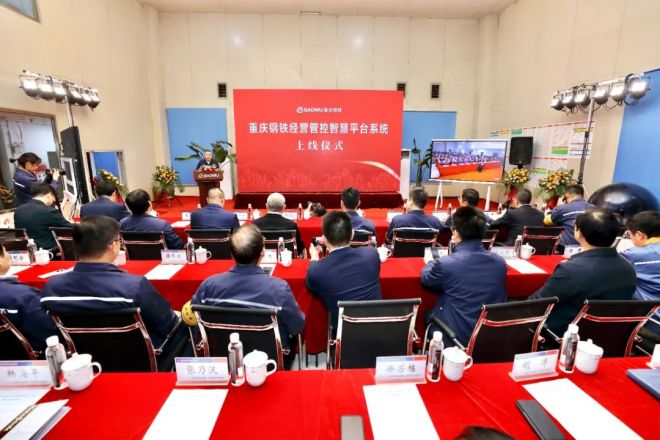
经营管控平台上线
2021年,重庆钢铁项目立项103项,计划投资额26.92亿元,其中智慧制造固定资产投资项目立项批复38项,计划金额5.38亿元。随着码头、料场、焦化、烧结、高炉工序能力提升项目全面建成投运,炼钢二系统配套的连铸机改造完毕,中板产线完成升级改造并恢复生产,棒、线产线相继完工,重庆钢铁智慧制造成果接二连三。
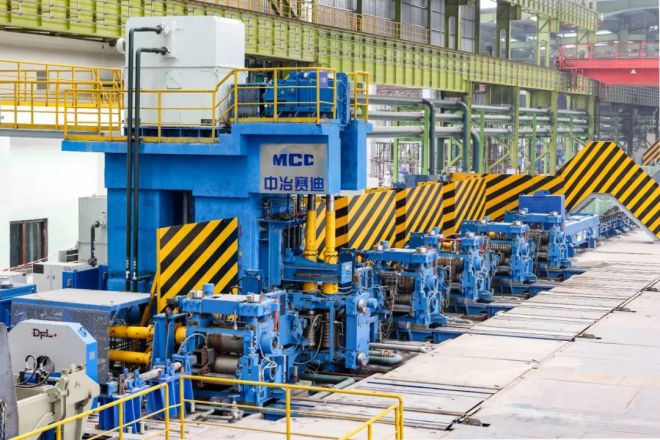
双高棒产线
2022年2月28日,重庆钢铁的“智慧产线”双高棒产线进入满负荷生产阶段。“智慧产线”双高棒产线采取一线一室集中操作控制,应用了物联网、大数据、云计算等新一代信息技术,采用了热送热装技术和热送直轧制技术、高效生产模块轧机技术、全线物料跟踪技术、自动控制技术、可视化管理等多项国内领先技术,具有信息深度自感知、智慧优化自决策、精准控制自执行等智慧制造应用场景,不仅生产效率比传统产线高,而且降低了工人数量和劳动强度,生产成本更低、质量更可控。
双高棒产线的成功投产是继重庆钢铁2700mm中板产线升级改造后,取得的又一个重要成果,作为重庆钢铁迈向智慧制造的标志性产线,该产线的投产达效标志着轧钢工序的升级改造全面结果。
智慧制造迈向“云时代”
除了开展智慧化升级改造,重庆钢铁充分发挥5G网络的大带宽、低时延、广连接的特性,依托5G核心专网,大步迈进“云时代”。
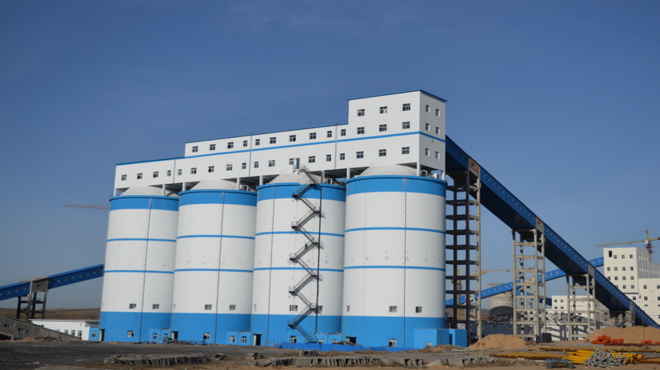
5G煤仓
2021年6月1日,5G+煤仓存料智能监测系统的数字经济应用场景在重庆钢铁落地。在重庆钢铁的5G煤仓存料智能监测系统上看到,凭借该系统,煤仓内的实时库存、物料堆放高度等实时数据一目了然,煤仓达到满仓高度后,系统便自动控制传送带停机,完全不需要人工操作。“5G+煤仓存料智能监测系统”采用成熟可靠的高精度、抗粉尘、立体多维度的无人智能煤仓物位巡检,改善了原有的料位测量模式,实现了煤仓巡检的无人化、智慧化。
“5G+煤仓存料智能监测系统”仅是重庆钢铁全面开启“经营管控智慧平台”建设的成果之一。
2021年10月31日,重钢经营管控智慧平台系统成功切换上线。应中国宝武“应上尽上”云服务功能的基本要求,该平台重构了15个信息化应用场景及功能,聚焦核心业务流程,融合了重庆钢铁经营管理、制造运行、现场生产执行的业务需求,实现了产、供、销业务的全面整合贯通,是“重庆钢铁的大数据库”,实现了全工序运行状态实时监测等功能。该平台的成功上线,是重庆钢铁智慧制造迈向“云时代”,加快推进智慧制造转型升级,推进“产业智慧化、智慧产业化”进程的重要手段。
2022年,重庆钢铁全力推动公司从“传统制造”向“数字智造”的转型,新增了16项智慧制造固定资产投资项目,投资总额达3.3亿元,其中,围绕区域全自动化、无人化投入1.6亿元。同时开启“万台宝罗”工业机器人应用倍增计划,2022年新增28台,2023年新增56台,2024年新增56台,2025年新增37台,2026年新增126台。确保操作室一律集中、操作岗位一律机器人、运维一律远程、服务环节一律上线等“智慧化指数”的不断提升。
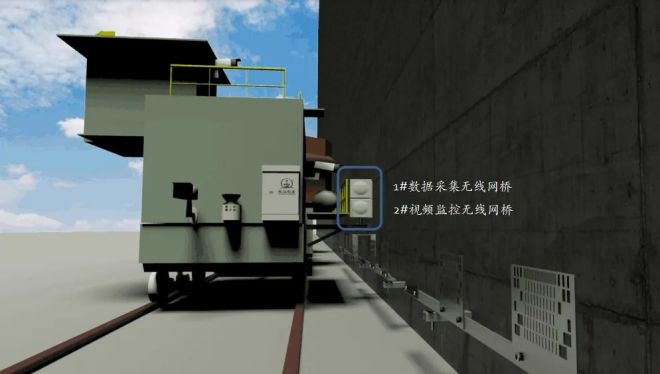
电机车无线数据通讯传输示意图
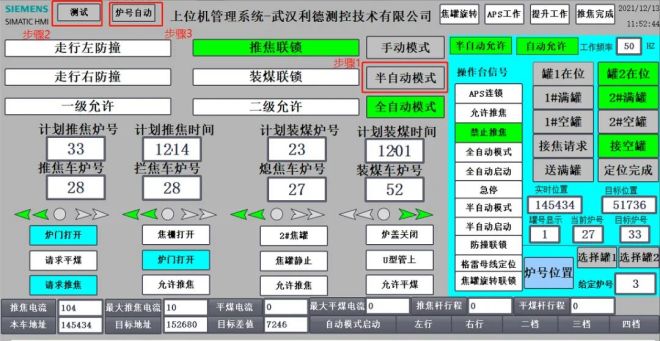
位于现场操作室的联锁控制人机界面
实现焦炉机车全自动操作是重庆钢铁实现全自动化、无人化的重项目之一。2021年5月,重庆钢铁启动了炼铁工序推焦车、拦焦车、装煤车、干熄焦车、水熄焦车的系统改造,2022年1月该项目进入功能测试阶段,2月开始试运行。该项目实现了焦炉作业机车的自动走行、自动对位、炉号识别等功能,最终实现电机车无人化操作、各车连锁推焦作业、电机车安全防护自动报警及视频实时监控。该项目的完结,标志着重庆钢铁朝着“数字化、网络化、智能化”迈进了一大步,开启了高质量发展新征程!
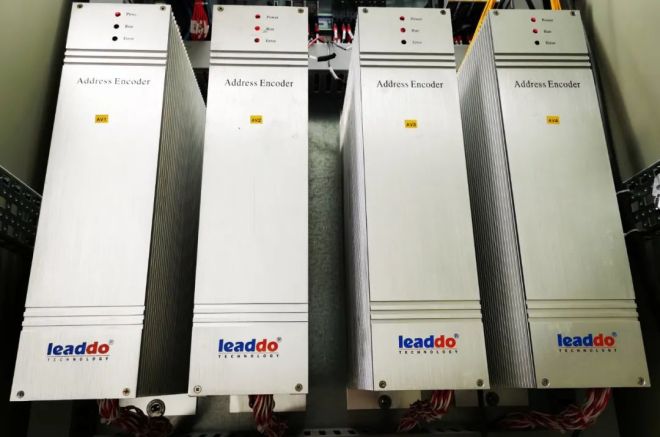
全新升级后的电机车地址检测单元
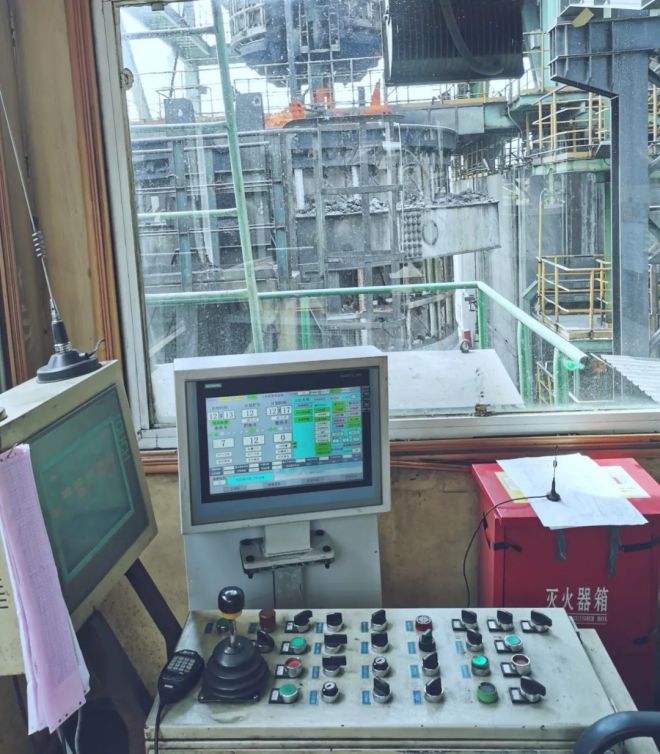
实现电机车无人化后的操作台