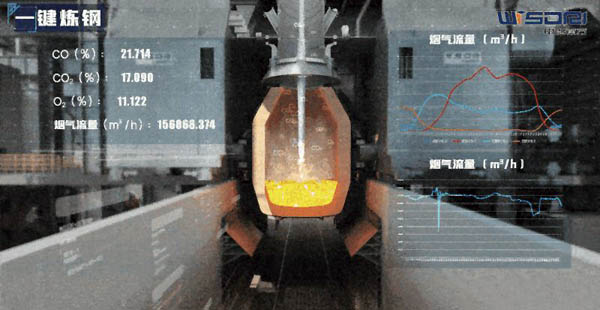
图为“一键”炼钢效果图。(中冶南方供图)
本报通讯员 南方
在2月28日《中国冶金报》5版发表的《炼钢,还可以更智能》一文中,通过一连串数据和一系列典型工程的直观展示,中冶南方“智慧炼钢一体化平台”降本增效的领先优势一览无余。这次,笔者以“高效化”和“高质量”为关键词,深入探寻中冶南方“智慧炼钢一体化平台”如何令炼钢更高效、更高产地生产出优质钢水的。
高效化生成与管理
聚焦“高效化”,中冶南方“智慧炼钢一体化平台”可令炼钢生产更高效:通过铁水智慧运输无人化操作,减少95%人为失误,保证生产顺畅;信号畅通,可适配各类通信基站,在错综复杂的钢结构厂房内,实现5G网络全覆盖;定位精准,采用自主设计的专用测量辊,配合激光测距,定位精度可达毫米级别;识别高效,配备激光扫描+视觉识别,自动对5米以内的建筑物和人员进行判别,实现声光提醒、人员保护、自动启停。
应用中冶南方“智慧炼钢一体化平台”,可实现废钢智能配料:省时省力,精准采集,精准分类,精准配料;可通过专家系统和图像识别技术,判定废钢种类,再由无人天车分区分类储存,并结合铁水情况和钢种要求,得到废钢配比及重量,自动配料。
应用中冶南方“智慧炼钢一体化平台”,可实现一键炼钢:缩短冶炼及出钢周期1分钟/炉,降低熔剂消耗5公斤/吨,命中率达92%,钢水回磷小于20ppm;可涵盖从智能炼钢到智能出钢的全过程自动操作——根据主副原料和钢种要求,实现自动加料、自动吹炼、副枪测温取样、烟气实时分析、滑板挡渣、下渣检测、车辆与转炉联动出钢、吹氩站氩花判别和机器人测温取送样等。
应用中冶南方“智慧炼钢一体化平台”,可实现物流/能流可视化:促进工序间协同生产,从出铁至连铸,各工序衔接总体减少2.3分钟;有效管控钢水温度,提高生产效率;通过智能定位、图像识别等技术,实现对钢铁罐和废钢料槽的全过程跟踪,进而实现对主物料的自动跟踪;建立从转炉出钢到连铸回转台的钢水温度预测模型,实现全流程钢水温度流管控,满足连铸生产的热度要求,可有效降低中间罐加热装备使用频率。
应用中冶南方“智慧炼钢一体化平台”,可实现排程调度可视化:优化生产组织效率,消除调度瓶颈,钢水接受跨行车转运时间减少5秒~10秒/炉次;对生产排程进行实时、动态调整,使生产计划与实际生产相匹配;根据实时排程及跟踪信息,自动协调各跨起重机的吊运作业,减少吊车“空跑”或“跟跑”,提高生产效率。
应用中冶南方“智慧炼钢一体化平台”,还可实现维护/管理便利化:提高检修及生产管理效率,实现生产透明化,保证安全生产;建立电子摘挂牌系统,在各类终端直观展示维护检修情况,实现设备的自动联锁、解锁;针对不同层级的管理人员,自动推送个性化的定制画面,支撑各级生产管理高效运行。
借助中冶南方“智慧炼钢一体化平台”,炼钢生产与管控的全过程效率显著提升。以2×120吨转炉为例,经测算可提升产量60吨/天,年提升产量达18000吨。
高质量的钢水生产
聚焦“高质量”,中冶南方“智慧炼钢一体化平台”在提高钢水质量方面也有“质量秘籍”——
“一键”操作:优质钢水背后的技术保障,严格把控炼钢过程中脱硫、精炼等各道关键工序,为冶炼优质钢水提供技术保障。
“一键”脱硫:铁损比人工操作降低10%,一次脱硫命中率≥98%;通过中冶南方自主研发的专有脱硫工艺模型,实现铁水罐倾翻车的自动行走、自动倾翻、自动扒渣、自动搅拌、自动加料、自动测温取样、自动出站等,并且可以识别铁水的成分数据,匹配相应的工艺参数,自主完成脱硫工序。
“一键”LF:一键投用率≥98%,成分合格率≥98%,温度合格率≥98%;系统内置电极升降、温度控制、合金微调、底吹氩等模型,通过生产数据自学习,不断完善自身模型,再配上电极自动更换和探头自动插、拔机器人,自主完成LF炉各项操作。
“一键”RH:一键投用率≥95%,成分合格率≥98%,温度合格率≥98%;实现从顶升开始、至破空结束的自动操作,包括液压顶升高度随真空室内真空度的自动调整,真空系统的自动脱气与破空,加料系统自动设定、称量与投料,提升气系统自动开始、结束与调整。
数据支撑:优质钢水背后的质量管控,多维度收集生产数据,跟踪溯源每一包钢水的生产情况,并将数据分析结果反馈至产线,进而优化生产操作,实现质量管控的有效提升。
钢水数字化:可重现钢水冶炼过程,为质量追溯、优化生产提供分析数据;分类储存不同炉次的操作、能源、质量、物料等数据,为精细化生产、质量回溯提供支撑。
质量/成本可视化:实时监控冶炼过程的质量、能源、辅料消耗情况,并生成各炉次工序的成本和质量评估;利用质量评定模型,实时显示炉次质量分值并预警;利用成本计算模型,实时显示炉次及工序成本,为钢厂降本提质打下基础。
中冶南方的“智慧炼钢一体化平台”既“高效化”又“高质量”,引领了炼钢生产全工序迈上智能化发展快车道,助力钢企降本增效、提质发展。
《中国冶金报》(2023年03月21日 05版五版)